Metsä Board's Kemi mill development programme completed
- Admin
- Sep 22, 2023
- 2 min read
Packaging Solutions
The development programme for Metsä Board's white kraftliner mill in Kemi has been completed in parallel with Metsä Fibre's new bioproduct mill. In addition to increasing the mill’s capacity by 40,000 tonnes per year, the development programme will reduce the mill's energy consumption by 5% and water consumption by around 40% per tonne produced.
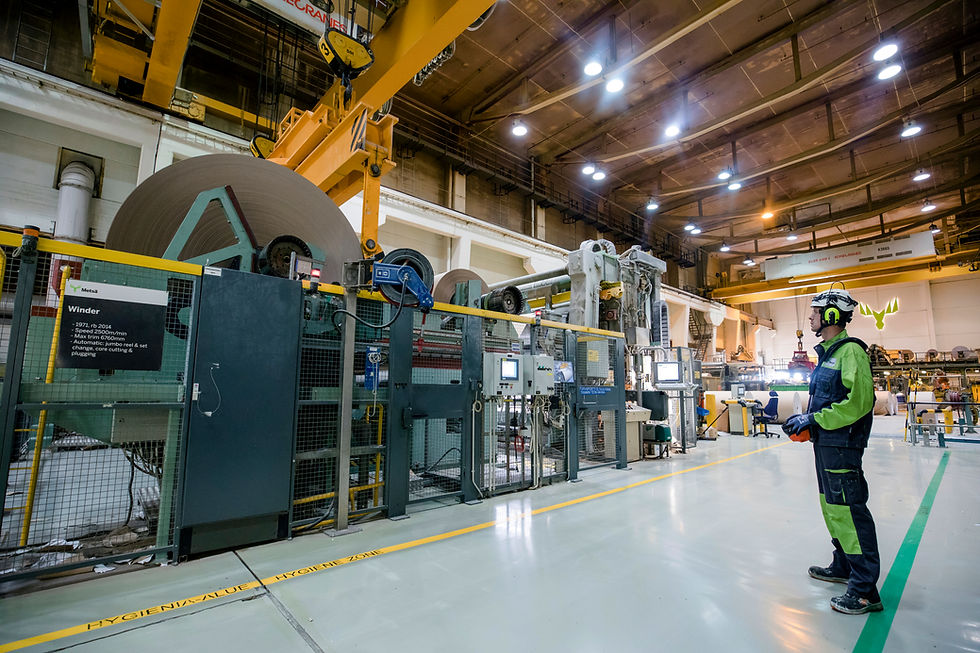
The Kemi paperboard mill is one of the world's largest producers of coated white top kraftliner and its products are used as a surface material for corrugated packaging worldwide. The development programme will increase Kemi’s annual production capacity of white kraftliners to 465,000 tonnes, with the majority being sold in Europe and North America.
The development programme for the board mill consisted of three parts: increasing the annual production capacity of white kraftliner by 40,000 tonnes, improving energy and water efficiency and transferring the unbleached pulp production line to Metsä Board.
A new, larger capacity disc filter has been built at the board mill, resulting in a more closed water circulation giving significant savings in water consumption. The mill's new heat recovery towers are more efficient at capturing waste heat from the process and recycling it back into the system. The supply of top layer birch pulp of the liner from the bioproduct mill as dried form will increase both the energy and production efficiency of the board machine.

To allow for the increase in production capacity, the board machine and finishing operations have been modernised and production has been streamlined. Examples of changes include the increase of the winder capacity, the automatic transfer of machine reels from the board machine to winder, fully automated reel loading and a new logistics chain between the deep water port of Ajos in Kemi.
As part of the development programme, Metsä Fibre's unbleached pulp production line will be transferred to Metsä Board in a modernised state. The production line will have an annual capacity of 180,000 tonnes of softwood pulp, which will be used in the bottom layer of the Kemi kraftliner.
‘Around the world, customers specify 'Kemi' when they mean high quality coated white kraftliner. Lightweight and durable kraftliners play an important role in reducing the carbon footprint of corrugated packaging. This investment meets our customers' needs by improving the availability of packaging materials with further improved environmental performance,’ said Mika Joukio, CEO of Metsä Board.