Packaging Solutions
Corrugated converters and their flexo plate suppliers can now enjoy the triple benefits of quicker plate production, improved graphic performance and reduced costs as Esko releases the latest version of its Print Control Wizard software to extend the tool with screening optimised for the post print corrugated market.
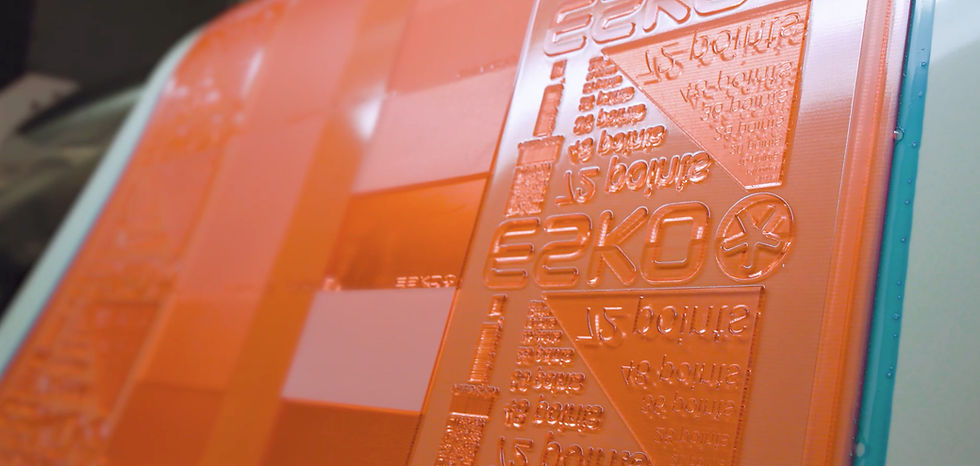
This new version of the software uses all critical print parameters and variables – imaging resolution, exposure settings, plate, substrate, anilox, press type and inks – to simplify the flexo platemaking process for post print corrugated packaging production. Print Control Wizard standardises the generation of microcells in the highlight areas of the plate.
‘Operators utilise an intuitive wizard style user interface that unlocks powerful functionality to quickly and easily create premium flexo plates,’ said Robert Bruce, RIP and screening product manager with Esko. ‘The Corrugated Crystal Screens address the problems associated with recycled board liners, giving corrugated post print converters the opportunity to improve print quality or if print quality is not a goal, reduce ink costs. The screens can be imaged using our latest CDI Optics 100 technology, allowing plates to be made at 10 m2 per hour. Utilising the Crystal XPS brings a new level of plate quality and consistency for the corrugated market. This is obviously a win for both trade shops and corrugated post print converters.’
Esko developed Print Control Wizard in response to industry calls to simplify the implementation of screens and dot gain curves.
‘Our goal was to provide flexographic experts with the tools to standardise and simplify screen and curve creation, enabling them to achieve the best quality results without additional steps and checks being added to the process,’ said Robert. ‘After Print Control Wizard was honoured with a number of top industry awards, we have been working tirelessly to develop the new enhancements, and we are delighted to now release this new version for the corrugated market as we continue supporting the work of print and packaging specialists across the industry.’
A beta testing partner of Esko, Contact Originators Group in Dukinfield, Manchester, is renowned for its innovative approach to packaging origination, graphics management and flexographic plate production. Operating across the UK and Europe, the company was the first flexo platemaking company in the UK to have gained Esko HD Flexo accreditation in the corrugated industry.
‘Corrugated is a highly competitive and technically challenging print sector,’ said Nick Mitchell, general manager at Contact Originators. ‘With lower grammage and recycled materials coming onto the market today to drive down costs, we need to be constantly seeking new ways to boost our customers’ print consistency and performance.’
‘Our job is to ensure our customers’ presses run as smoothly as possible with maximum graphic impact,’ continued Nick. ‘This is where Print Control Wizard steps in.’
Esko Print Control Wizard reduces press stops for plate cleaning and make ready times, boosting overall equipment efficiency. It also enables printers to move to fixed palette printing due to the consistency the software brings on platemaking.
Les Jones, print innovation manager at Contact Originators, added: ‘What we have seen with Print Control Wizard is that plates are now more consistent, and we can produce them more quickly, which is great for a busy pre-press environment like ours. However, it is the benefits to our printer customers – and their customers, the brands – that really makes the software stand out.
‘We are seeing more colour density for less ink laydown on low grammage substrate, while printers are reporting they are achieving improved final print results in less time, with associated improvements in material and ink waste – a real bonus in today’s cost and sustainability focused industry.’
‘We estimate that Print Control Wizard is enabling our customers to save up to 20% on ink formulation too,’ added Les. ‘Working in partnership with them, we are seeing more precision on each job enabling less rework or waste, and using Print Control Wizard they can print solids, tone and test work from a single plate. In real terms, this means they are making savings on the number of plates used, as well as reducing set up times and ink consumption.’
Comentarios