Print Solutions Green Solutions
Canon has announced that it will begin using recycled steel material (electric furnace steel sheets) in some printing products, including office multifunction devices (MFDs), home inkjet printers, large format inkjet printers and commercial printing presses, that will be released in 2025. Going forward, the company will gradually increase the number of products utilising recycled steel.
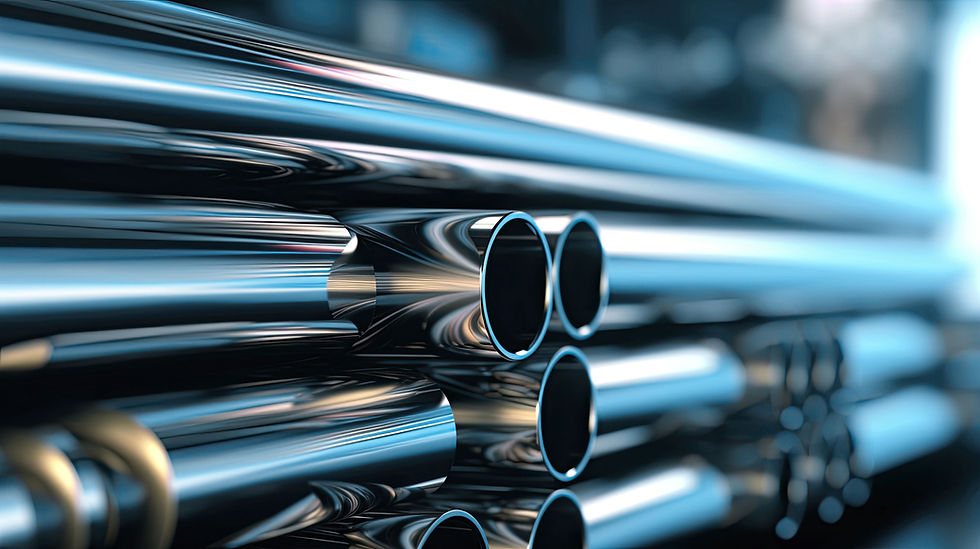
Electric furnace steel sheets are recycled materials produced in an electric furnace from steel scrapthat has been collected from used products. Its use thereby reduces the input of new resources andincreases the resource recycling rate.
Furthermore, since CO2 emissions from the production of electric furnace steel sheets are about one-fifth of those from blast furnace steel sheets – common steel materials made from iron ore – their contribution to decarbonisation is attracting attention. Steel is the second most used material by weight in Canon's printing products, following plastic. The company has studied the characteristics ofelectric furnace steel sheets and optimised the processing method so that they could be used inproducts.
The production of electric furnace steel sheets requires steel has been thoroughly separated fromother materials including plastic and copper. Currently, Canon Ecology Industry, one of the group companies, finely separates steel scrap from collected used office MFDs and sells the refined steel scrap to Tokyo Steel Manufacturing, an electric furnace steelmaker. The total amount of collected steel scrap provided to Tokyo Steel from April 2020 to March 2024 was more than 5000 tonnes.
Canon will supply steel scrap, and in turn use the electric furnace steel sheets produced by Tokyo Steel to develop, design, and manufacture more sustainable products thereby promoting the recycling and effective use of limited resources.
Since 1988, Canon has adopted the corporate philosophy of Kyosei and based on this philosophy has been at the forefront of initiatives to protect the environment to build harmonious relationships with the Earth and the natural environment. Since 2008, the company has been working to achieve an annual average improvement of 3% in lifecycle CO2 emissions per product. As a result, since 2008 it has achieved an average annual rate of 3.95% (2008 to 2023) and a cumulative improvement of 44.4%. It will continue working to cut its CO2 emissions across product lifecycles and aims to achieve net zero emissions by 2050 through various activities.