Packaging Solutions
Colton Packaging has worked with long standing manufacturing clients to support them with ‘going green’ in their protective packaging to create a 100% recyclable solution.
In response to its clients wanting to be more sustainable and reduce waste, Loughborough based packaging specialist, Colton Packaging, has completely eliminated polystyrene from the corner packaging used to protect a manufacturer’s door and frame products.
With over 20 years’ experience, Colton’s in-house design team relished the opportunity to reimagine the bulky, polystyrene corner pieces whilst giving them a sustainable edge. The challenge was finding a replacement that was as robust in protecting the products, while being eco friendly, minimising waste and reducing required storage.
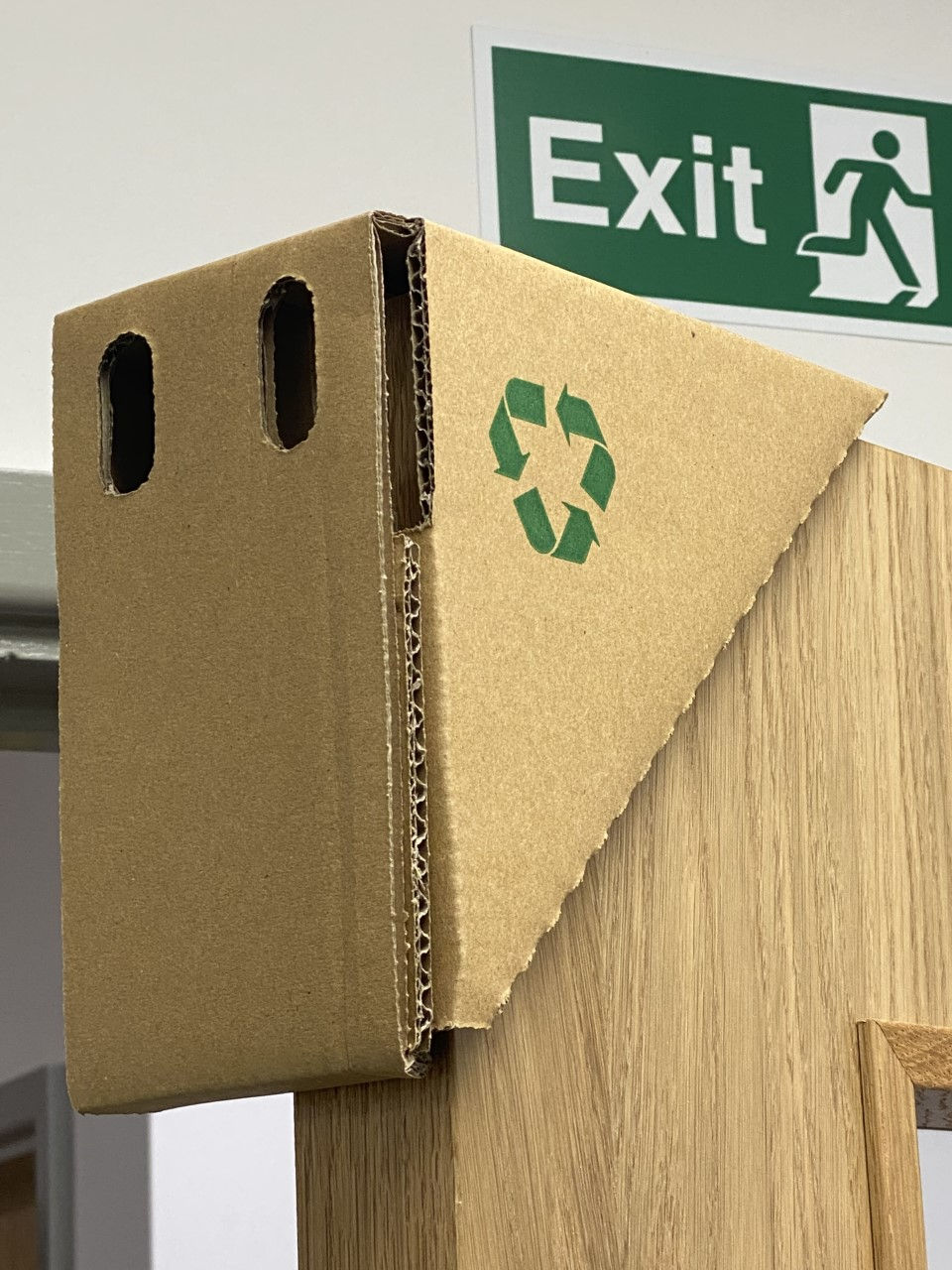
Colton’s head of design Ross Connolly commented, ‘The polystyrene pieces are bulky to store and also cannot be recycled so are costly in terms of waste. With our expertise in corrugated cardboard packaging, we wanted to create a solution made from recycled material that is also fully recyclable itself.
‘Using the original parts as a template, we visualised the pieces as flat scored, corrugated sheets and created designs for bespoke recyclable corrugated cardboard inserts. We went through a few iterations with the clients utilising various CAD drawings and prototypes. We soon settled on designs which are flat pack to store and easily folded into 3D protective corners which slot on doors and window frames.’
To cater for different thicknesses of product an additional insert was created to prevent any movement during delivery and transportation. Different versions with protective buffers were also created to accommodate protruding sections.
‘Using the original parts as a template, we visualised the pieces as flat scored, corrugated sheets and created designs for bespoke recyclable corrugated cardboard inserts. We went through a few iterations with the clients utilising various CAD drawings and prototypes. We soon settled on designs which are flat pack to store and easily folded into 3D protective corners which slot on doors and window frames,’ he said.
To cater for different thicknesses of product an additional insert was created to prevent any movement during delivery and transportation. Different versions with protective buffers were also created to accommodate protruding sections.
The flat pack corrugated cardboard solution has 100% replaced polystyrene and delivered multiple additional practical and carbon saving benefits to the whole packaging process.
Ross explained, ‘In terms of materials, the clients are seeing around a 30% reduction in costs. In addition, the new flatpack design takes up less than 25% space than before. So, in our stock and serve warehouse, where the polystyrene sections were taking up a full load, they now only need two pallet spaces for storage. The same goes on the lorries. The clients were receiving two dedicated lorry load deliveries per week from full 18tonne trucks. They still have two drops per week, but now we can fit them into other delivery schedules, therefore reducing mileage and subsequently fuel consumption.
‘Above all though, they have 100% removed polystyrene, eradicated waste and replaced it with a 100% recycled and recyclable solution, without compromising on quality and product protection. In fact, corrugated cardboard offers the same or potentially better protection than polystyrene, as it does not snap and holds its form on impact.’
Since the new protective corrugated cardboard solutions have been implemented the clients have achieved a significant cost reduction and improved sustainability credentials. These benefits are also being multiplied across the end users, as on building sites where residential developments are receiving the doors and frames, they can achieve zero waste to landfill and improve recycling from packaging.