GPI Leeds achieves top VLF overall equipment efficiency award
- Admin
- Mar 29, 2019
- 2 min read
Packaging Solutions
Heidelberg has awarded packaging printer Graphic Packaging International (GPI) Leeds a presentation press gear in recognition of its high productivity. The company, the first in the UK to install an 18,000 sheets per hour Speedmaster VLF press, has the highest Overall Equipment Efficiency of any VLF Heidelberg plant in the world.
The company has two Speedmaster presses, an XL 145-6L which has broken the 70 million sheets a year barrier and an XL 145-6LYYL which is recording over 68 million sheets a year. Both presses run 24 hours a day, six days a week and have an average run of 20,000.
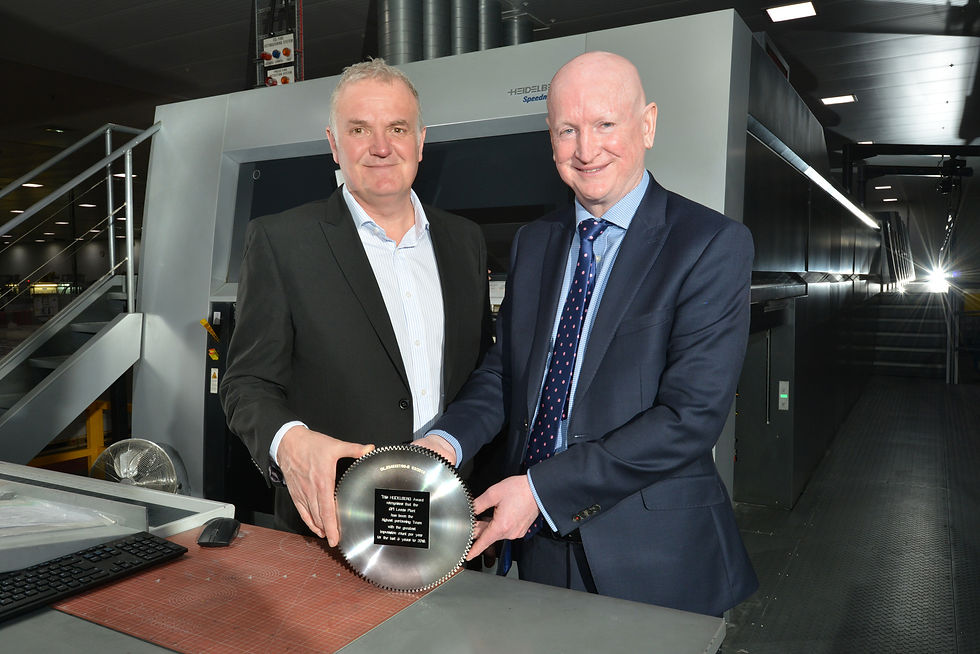
The presses are elevated, with automatic pile changes at feeder and delivery. A bespoke logistics system, custom designed by Krifft and Zipsner, takes pallets of board and finished work to and from the Speedmaster presses.
GPI Leeds produces cartons that can be seen in every major supermarket in the UK. Its products cover cereal, tea, confectionery, chilled and frozen products, whisky and more.
Plant manager Dean Naylor attributes the productivity to standard ways of working, planned organised workflow, good prepress preparation, an extremely structured approach to all aspects of the business and a strong teamwork ethic and mentality.
‘The operators and the inter departmental support teams are the most important part. We liken the teams to having the Formula 1 pit stop mentality on all make readies,’ said Dean Naylor.
Operators at GPI Leeds take advantage of Heidelberg refresher training twice a year during maintenance visits. Heidelberg service is highly prized by the company. ‘Heidelberg UK reacts extremely quickly to any issues that arise. They understand the importance of the presses to our business and the best compliment I can give them is that they react and give an equal importance to the issues as we do.’
High productivity has to be achieved with no compromise to quality, something that is underpinned by the use of InpressControl for inline colour and register control and Saphira pressroom consumables from Heidelberg.
‘Our quality has improved over the last three or four years. We will not sacrifice quality for speed so we have to ensure we have the correct processes and procedures in place to achieve both quality and high efficiencies in equal measure,’ he said.
Food packaging brands must, of course, be instantly recognisable and have shelf appeal. GPI Leeds scored an AA rating when recently audited by BRC and scored 905 out of 1000 in an AIB audit, its highest score to date. These are both certifications for food safety. The company also holds an ISO 12647-2 colour accreditation.
‘High productivity helps us maintain shorter turnarounds on customer orders, particularly during peaks of high demand. It also helps us maximise the utilisation and output of the presses. Our customers expect reliable service as a prerequisite which is what we expect from our equipment,’ said Dean.