Esko simplifies flexo platemaking
- Admin
- Jun 8, 2018
- 3 min read
Packaging Solutions
Esko has introduced two new solutions – the CDI Crystal 4835 and Print Control Wizard – taking its ‘Flexo Simplified’ offer to a completely new level.
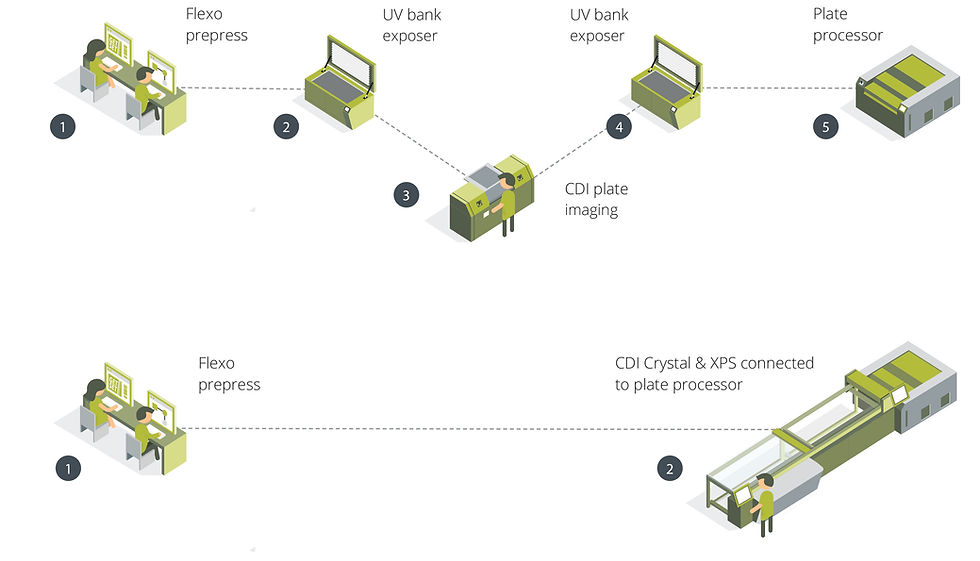
Flexo platemaking, in most cases today, is a process with many manual steps that require highly skilled operators to produce the right plate for the right job. These new launches mark the first and only automated flexo platemaking line in the industry, and to streamline the entire process, Esko has made it more automated and much easier to use. This not only improves the productivity of platemaking, it also ensures quality and consistency throughout, and simplifies flexo platemaking considerably.
Esko follows the successful introduction of its CDI Crystal 5080 flexo imager with the introduction of the CDI Crystal 4835. This new launch supports the 48 x 35 inch plate size that is popular with flexo converters and provides the same benefits as the CDI Crystal 5080. The Crystal CDI features automatic plate loading and unloading and is very easy to use. Users report significant benefits in both time and quality. Operators need minimal training and spend 50% less time at the device. In addition, plate waste and plate inconsistencies resulting from manual plate handling are completely eliminated.
The innovative XPS Crystal exposure unit has been introduced for both the 5080 and 4835 sizes in the past few years. These systems reduce the manual steps from nine steps to just one.
Using the CDI Crystal in combination with the Crystal XPS frees up operators from mundane and repetitive tasks. It also means that there is only a single system to monitor.
The new Print Control Wizard software adds a new level of simplification in the platemaking department. Esko has worked its decades of expertise into an easy to use wizard that takes the complexity out of flexo platemaking. Flexo platemaking is now easier to use and easier to learn for everyone, without the need to hire dedicated flexo platemaking experts.
The application goes beyond excellent screening and outputs the right plate fit for purpose based on a range of print run parameters. The plates produced through Print Control Wizard deliver superior print quality; they use a screen and dot gain curves that take into consideration the press, substrates, inks, anilox and other print run parameters.
‘The first customers that worked with Print Control Wizard confirm that it is as simple as entering the production parameters in order to get superb screening fit for the print run,’ said Robert Bruce, flexo product manager with Esko, ‘and the print results prove it: the plates last longer on the press and deliver brilliant, consistent quality.’
Esko’s innovative Crystal line delivers flexo plates with unmatched quality and consistency for all flexo printing applications. The benefits build up along with the configuration:
CDI Crystal standalone for ultimate ease of use and plate waste reduction.
CDI Crystal combined with the Crystal XPS adds automation and unparalleled plate consistency.
CDI Crystal XPS combined with Print Control Wizard adds flexo know how out of the box. With this configuration, you can automate the production of consistently high quality plates without the need for platemaking experts.
‘Esko has always and will continue to protect customers’ long term investments,’ said Pascal Thomas, director pre-press and platemaking. ‘With these three Crystal quality levels, we offer a transparent and modular growth path for our customers, who can decide what level of quality and automation best fits their business.’
The combination of the Crystal CDI 4835, XPS 4835 and Print Control Wizard delivers the highest possible quality flexo print results available in the industry today. ‘As run lengths and deadlines get shorter, converters and pre-media need to continuously improve efficiency,’ explains Geert De Proost, director solutions marketing at Esko. ‘By expanding our flexo solution portfolio with these innovations, we simplify flexo platemaking even further. Today it comes yet another step closer to be a simple ‘push the button’ solution.’