Beamglow invests in UK’s first Bobst Masterfold 110 securing premium quality
- Admin
- May 8, 2018
- 2 min read
Packaging Solutions
With more than 50 years experience in high quality manufacturing of luxury cartons for the premium alcohol, fine fragrance and cosmetics packaging markets, Cambridgeshire based Beamglow has announced its investment in a new Bobst Masterfold 110.
‘We know that the industry will assume we are investing in this technology for output and productivity reasons. However, the truth is that this is all about quality control and consistency of production for what are exacting market needs,’ said James Griffin, Beamglow operations manager.

Luxury packaging markets demand acute attention to quality and Beamglow is proud of its record and enviable reputation for achieving high performance production. We demand perfection and minimise waste and errors at all times to effect just in time manufacturing. The new Masterfold investment simply adds to our ability to further deliver excellence in quality, service and support for our strategic clients.’
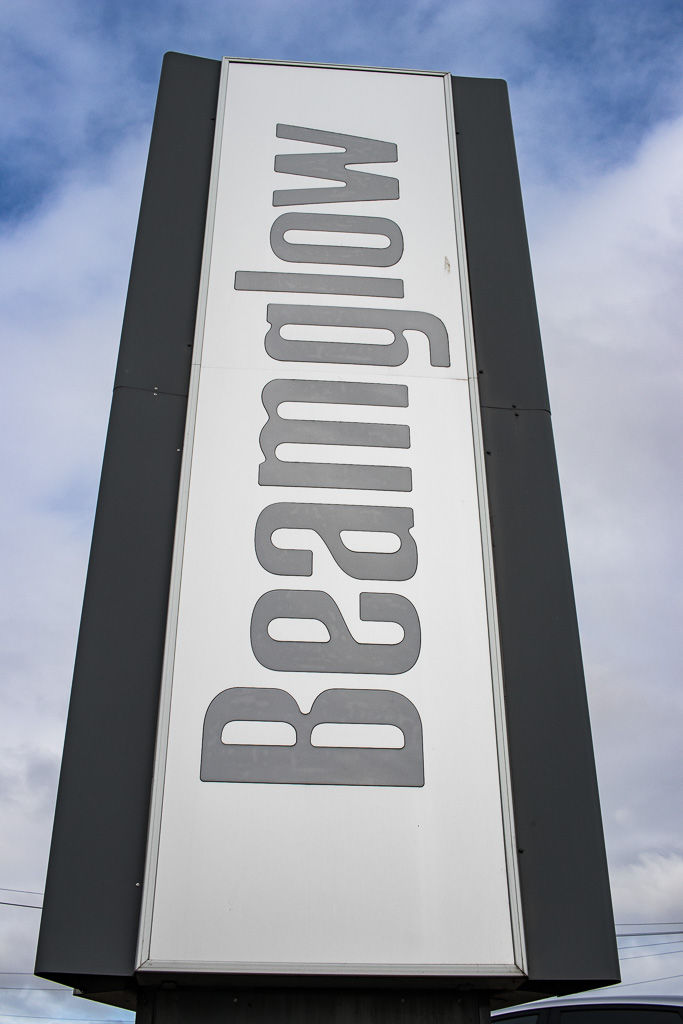
The Masterfold 110 follows a series of investments in the business, including an increase in foiling and die cutting capacity to increase throughput and enhance client care and satisfaction.
Notably the all new Bobst machine is designed to run up to 700 metres per minute, has a 15% faster set up time and increases throughput by 10%. This adds versatility in the types and styles of packaging Beamglow can handle. With operator safety also front of mind, the new design has a 10% reduction in noise compared with existing models.
James added, ‘The business has developed significant expertise in delivering shelf stand out for our clients and we are at the forefront of our industry pioneering quality standards for the sector. We work in partnership with our clients to understand their current and future needs and recognise that continual investment in our assets drives our market leading position.
‘This new investment, with its game changing focus on production quality and consistency, will give us the peace of mind that we can continue to drive our standards even higher whilst maintaining our manufacturing flexibility.’