DS Smith takes further step to lead on sustainability
- Admin
- May 4, 2018
- 2 min read
Green Solutions
One of DS Smith's corporate goals is to lead the way in sustainability.
The company has already hit its 2020 targets to reduce its CO2e per tonne and its water effluent per tonne of production, and is pleased to now announce the results of a collaboration between DS Smith’s Plastics and Paper Divisions, which transforms plastic rejects from the papermaking process into a new raw material for plastic production.

A number of DS Smith's paper mills across Europe have run projects to explore the potential of plastic rejects from the papermaking process. The company has previously discussed how its Kemsley paper mill in the UK uses its plastic rejects as fuel for the mill's on-site energy recovery facilities, which help to make the papermaking process more sustainable.
Another project, at Aschaffenburg Mill, Germany, is now providing the raw material for DS Smith Plastics' production processes in Croatia, which creates products from paper mill waste. By transforming its waste into a resource, the company is closing the loop on both paper and plastics within the group's operations, ensuring that plastic rejects are dealt with higher up the waste hierarchy and given another useful life.
Aschaffenburg Mill separates plastic rejects out from the papermaking process, and sends the useable fibre back into the paper mill. The plastics that are separated out are turned into a new raw material, which is used by the Plastics Division in Karlovac, Croatia, in its Beaulex product.
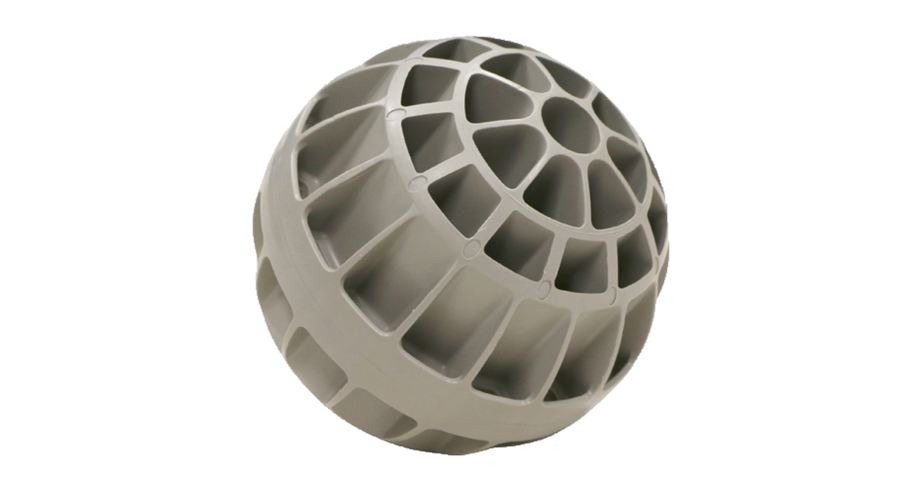
Beaulex is used in rainwater buffering systems to manage the absorption of rainfall in urban spaces, preventing flash flooding on sites like car parks. As the product of a closed recycling loop within the DS Smith Group, it is made entirely from the post consumer plastic recovered from its mills.
Lucas van der Schalk, chief operating officer for DS Smith Plastics, said:
This ambitious project brings our Plastics and Paper Divisions closer together as we work to lead the way in sustainability. Across our mills, we are exploring ways of using plastic waste within the group. This particular success story of recycling the plastic waste from Aschaffenburg Paper Mill's papermaking process into the raw material into products in Croatia is a tangible example of closing the loop on material streams and increasing resource efficiency across DS Smith.’